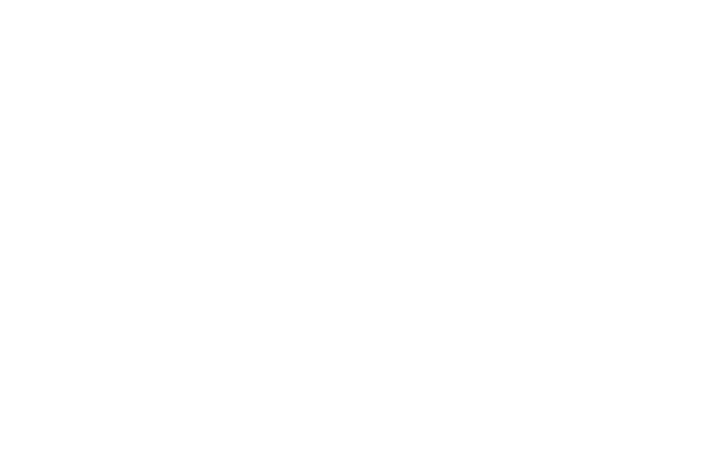
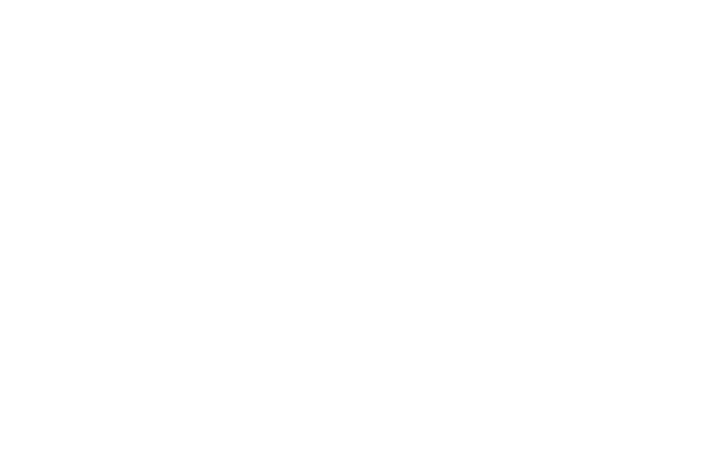
WMS and MES for the Furniture Industry
Operational efficiency, multi-flow management and advanced automation
Some industries require the synchronized management of multiple, highly diverse operational flows. This is especially true for the Furniture Industry, where companies must handle a wide range of activities—from storing materials of various shapes and sizes, to line-side assembly and component replenishment, all the way to packaging and shipment. With the rapid growth of e-commerce, optimizing every stage of the logistics and production chain has become essential to ensure high service levels and meet increasing customer expectations.